Improving the Energy Efficiency of Palm Oil Equipment in the Food Industry
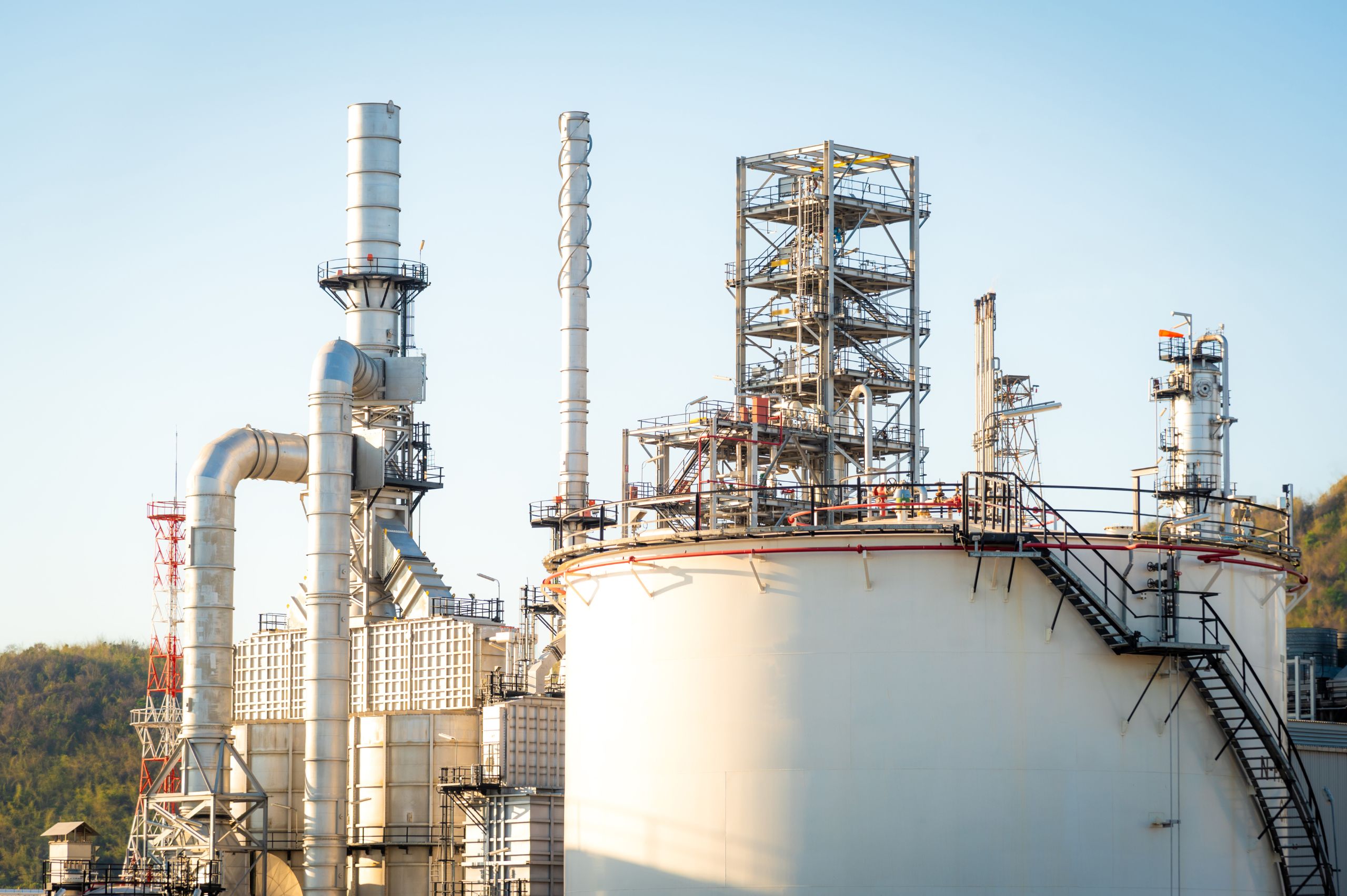
Energy efficiency is becoming a top priority for food manufacturers, not only to reduce operational costs but also to meet environmental and sustainability goals. In the palm oil industry—particularly where palm oil is processed for food-grade applications—significant energy is consumed during sterilization, digestion, pressing, and refining. Optimizing the energy performance of palm oil processing equipment can lead to substantial savings and increased competitiveness. This article explores practical strategies to enhance energy efficiency in palm oil equipment, with a focus on critical machinery like the vertical digester, and highlights the role of the right food processing equipment supplier in achieving these goals.
Why Energy Efficiency Matters in Palm Oil Food Processing
Producing palm oil for food applications involves energy-intensive steps, especially in high-capacity facilities. High energy consumption is a result of electric motors, heat exchangers, steam systems, and boilers. If not managed effectively, these systems can lead to excessive operational expenses, high carbon emissions, and waste of valuable resources.
In today’s climate-conscious food industry, buyers and regulators expect manufacturers to adopt greener practices. In addition to reducing production costs, increasing energy efficiency enhances a business’s standing as a sustainable food supplier.
Identifying Major Energy Consumers in Palm Oil Processing Lines
The most energy-intensive sections of the operation must be identified in order to increase energy efficiency. These typically include:
Sterilization Systems: High-pressure steam boilers are required to sterilize fresh fruit bunches (FFBs). These systems often consume the most thermal energy in the plant.
Vertical Digester: The digester uses steam and mechanical agitation to soften fruit and prepare it for pressing. It requires both thermal and mechanical energy.
Oil Pressing Machines: Motors and hydraulic systems consume significant electricity during continuous operation.
Refining Units: Processes like deodorization and bleaching rely on high-temperature operations and require consistent energy input.
Drying and Storage Equipment: Preserves oil quality and avoids contamination by using heat and fans.
Energy-Efficient Strategies for Palm Oil Equipment
Improving energy efficiency requires a combination of equipment upgrades, operational changes, and monitoring systems. Here are a few of the best techniques:
1. Make use of heat recovery systems and boilers that use less energy.
Switching to high-efficiency biomass boilers or dual-fuel systems can reduce fuel use during the sterilization and digestion process. Additionally, installing waste heat recovery systems allows you to reuse thermal energy from flue gases, condensate, and steam lines. This reduces the fuel needed to reheat water and generate steam.
2. Upgrade to Modern Vertical Digesters
Older digesters are often energy-intensive and prone to heat loss. Investing in a modern, insulated vertical digester reduces thermal leakage and improves heat transfer efficiency. Additionally, some vertical digesters use variable frequency drive (VFD)-equipped automated agitation systems that provide precise motor speed control and reduced electricity consumption.
3. Choose High-Efficiency Motors and Pumps
Motors used in oil presses, conveyors, and pumps should meet IE3 or higher energy efficiency standards. The amount of electricity used can be greatly reduced by swapping out old motors with more efficient units. Additionally, by adjusting motor speed to process demands, VFDs maximize energy use.
4. Implement Process Automation and Control Systems
Automated control systems monitor temperature, pressure, and energy use in real time. This allows for dynamic adjustments that avoid overheating, over-processing, or running equipment under inefficient conditions. Automation ensures that each part of the palm oil processing equipment operates at its most efficient point.
5. Insulate Equipment and Pipelines
Heat loss through uninsulated surfaces leads to unnecessary energy waste. Applying proper thermal insulation on boilers, steam lines, digesters, and storage tanks helps retain heat and improve energy efficiency, especially in tropical climates where equipment is exposed to ambient moisture.
6. Recover and Reuse Condensate and Steam
Reclaiming hot condensate from steam-driven equipment like the vertical digester and reusing it in boilers saves energy and water. Installing steam traps and condensate return systems can improve overall thermal efficiency in palm oil processing facilities.
7. Regular Maintenance and Equipment Calibration
Energy losses often stem from poor maintenance—leaky steam lines, blocked filters, and misaligned motors all reduce system efficiency. Establishing a routine maintenance schedule, including calibration of sensors and cleaning of heat exchangers, ensures all equipment performs at optimal levels.
The Function of a Supplier of Food Processing Equipment
Choosing a knowledgeable and experienced food processing equipment supplier is vital for achieving energy goals. The right supplier can offer:
Custom-designed energy-efficient equipment: Tailored systems like heat-optimized digesters or low-energy oil presses designed to suit your processing needs.
Energy audits and consulting services: Technical teams can help evaluate your current setup and recommend energy-saving upgrades.
After-sales training and support: Proper training ensures your staff operates the equipment correctly and maintains it for peak performance.
Upgrades and retrofits: Suppliers often provide energy-efficient upgrades for older systems, allowing you to modernize without completely replacing your setup.
Working with a reputable supplier ensures you get more than just machines—you gain a partner in sustainable growth.
Looking Ahead: Toward Greener Palm Oil Processing
As demand for sustainable food oils grows, energy-efficient palm oil production will become a critical differentiator in the marketplace. Future-ready processors are already exploring options like:
Solar-assisted boilers
Biomass-powered generators using palm waste
Smart factory systems for full energy integration
These innovations are reshaping how food-grade palm oil is produced, allowing manufacturers to cut emissions, reduce costs, and meet increasingly strict food industry standards.
Final Thoughts
Energy efficiency in palm oil processing is not just a trend—it’s a necessity. By upgrading palm oil processing equipment, optimizing systems like the vertical digester, and partnering with the right food processing equipment supplier, food manufacturers can significantly reduce energy use, lower operating costs, and enhance sustainability.
With the right approach and technologies, producing palm oil for the food industry can be both profitable and environmentally responsible.